L’impact environnemental de la production d’acier et les avantages du recyclage
Selon le « Planétoscope », chaque tonne d’acier produite génère l’équivalent de 1,6 tonne de CO2. Cette pollution ne provient pas directement des matières premières qui sont d’origine naturelle. En réalité, si l’acier obtient un si mauvais résultat, c’est parce que son processus de fabrication et de transformation est lourdement consommateur en énergie. Toutefois, l’acier présente un avantage non négligeable : il est recyclable à l’infini, sans altération de ses propriétés. Le recyclage de l’acier s’avère donc une solution efficace pour réduire le bilan carbone de ce matériau, qui est l’un des plus utilisés au monde !
Introduction
En 2017, le taux de réutilisation de l’acier et de la fonte en France était de 49 % et de 50 % pour les matériaux non ferreux (cuivre, aluminium, zinc, etc.). Sur 18,3 millions de tonnes d’acier recyclé (tous métaux confondus), 9 millions de tonnes ont réellement été recyclées. Bien que ce ratio puisse paraître faible, son impact environnemental est en réalité élevé.
En effet, 1 tonne d’acier recyclé permet d’éviter 57 % des émissions de CO2 et 40 % de la consommation énergétique nécessaire pour la production de 1 tonne d’acier primaire. Ainsi, le recyclage des métaux ferreux (acier et fonte) a permis d’économiser 31 TWh de consommation d’énergie, soit l’équivalent d’environ 3 villes comme Lille. Quant à l’aluminium, qui est également un produit hautement recyclable, sa revalorisation a généré l’équivalent de 12 TWh de consommation d’énergie. Tous ces chiffres proviennent d’une étude réalisée par l’ADEME en 2017.
Si l’acier est recyclable à 100 %, alors pourquoi le taux de réutilisation n’atteint-il pas un niveau plus élevé ? En réalité, le recyclage de ce matériau se heurte à un effet contre-productif : l’acier recyclé coûte parfois plus cher à produire que l’acier fabriqué à partir du minerai de fer. Bien que potentiel de recyclabilité soit énorme, cet aspect économique constitue un frein au développement de cette filière. Des solutions d’économies d’échelle devront donc être trouvées à l’avenir pour favoriser de manière plus significative le réemploi de l’acier.
Où et quoi recycler dans l’acier ?
L’acier est partout ! Il est utilisé dans le secteur de l’automobile pour la fabrication des machines industrielles, des carrosseries de voitures ou encore des moteurs. Dans le domaine du bâtiment, où il est souvent combiné au béton ou pour créer des conduites d’eau ou de gaz, par exemple. Mais il est également présent dans la vie au quotidien : emballages alimentaires, appareils électroménagers, objets de bricolage, etc. Le recyclage de ce matériau concerne donc tout le monde, du particulier à l’industriel, sans exception !
Les sources de l’acier recyclé : le recyclage des produits finis
Tout est récupérable dans l’acier :
- Les emballages métalliques ;
- Les appareils ménagers ;
- Les véhicules de toutes sortes (voitures, camions, bateaux, avions, etc.) ;
- Les armatures structurelles pour béton ;
- Les éléments de construction d’un bâtiment (fenêtres, portes, gouttières, etc.) ;
- Les ponts, les statues, etc.
Les sources de l’acier recyclé : les déchets métalliques des usines
Si le recyclage de l’acier sert généralement à récréer d’autres objets en métal, certains déchets présentent d’autres particularités. C’est le cas notamment des rebuts de production et de transformation.
Les laitiers
Les laitiers ou « scories » sont des « co-produits », c’est-à-dire qu’ils sont indissociablement créés à partir de la fabrication d’un autre produit. En brûlant à haute température du minerai de fer ou du ferromanganèse, les constituants non métalliques et non gazeux se liquéfient. La fonte étant plus dense que le reste de ses composants, elle se sépare par gravité. Le laitier remonte alors à la surface où il est récupéré. Ce laitier peut provenir des hauts fourneaux, d’aciéries électriques ou d’aciéries de conversion (convertisseur).
Il existe 2 types de laitiers :
1 – Le laitier cristallisé, qui est obtenu par refroidissement lent. La matière est redirigée soit par un système de rigole depuis le haut fourneau vers une fosse, soit par des poches sur rails pour être déversée plus loin. Pour maximiser sa surface d’échange avec l’air ambiant, le laitier est épandu en faible épaisseur sur le sol. En refroidissant, ce dernier se solidifie formant ainsi des fragments denses de 0 à 300 mm d’épaisseur.
Le laitier cristallisé, après concassage, peut être utilisé en remblai ou en couche de forme pour la création de routes. Mais, il peut également servir de granulats pour béton, par exemple.
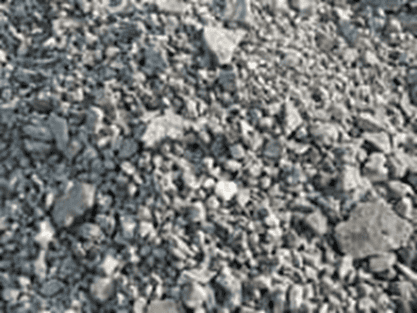
2- Le laitier vitrifié, qui subit un refroidissement rapide. Le laitier encore en fusion est refroidi avec de l’eau sous pression. Cette technique est dite de « granulation ». Une autre méthode dite de « bouletage » consiste à ajouter simultanément de l’air avec de l’eau.
Le laitier prend ainsi la forme d’un sable de 0 à 4 mm d’épaisseur. Le laitier vitrifié est récupéré par les cimenteries à des fins multiples :
- Pour constituer un liant hydraulique routier ;
- Pour produire du ciment, en remplacement du clinker ;
- Pour la fabrication du béton, en remplacement du ciment. Le laitier est alors préalablement broyé finement.
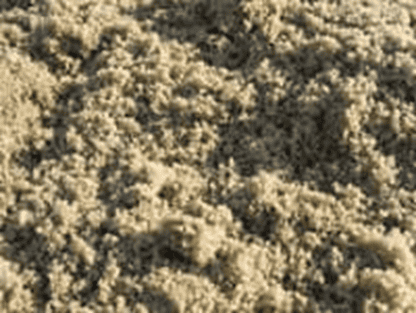
Les sables de fonderie
Pour former des pièces en métal, la fonderie utilise des moules en sable. Ainsi, on chauffe le métal jusqu’à sa température de fusion et on le coule dans l’empreinte du moule, dont la forme varie selon le type de pièces souhaité. Ce sable contient principalement de la silice, de l’argile, de la résine et des fines poussières. On réutilise les sables de fonderie recyclés comme matière première pour fabriquer du ciment de Portland. On peut également les mélanger avec du ciment pour créer un mortier de maçonnerie. Enfin, on les réemploie parfois comme substituts aux agrégats fins dans le mélange d’asphalte pour la construction de trottoirs ou de parkings.
Ces sables de fonderie peuvent se récupérer de différentes manières :
- Par voie humide (par jet d’eau). Cette méthode présente l’avantage de ne pas générer de poussières. Toutefois, l’eau de lavage doit être épurée avant d’être rejetée dans son milieu naturel pour éviter de contaminer les nappes phréatiques ;
- Par voie sèche (traitement mécanique). Le sable est criblé pour éliminer ses impuretés (parties métalliques). Les blocs de sable sont concassés et broyés ;
- Par voie thermique. Le sable est brûlé dans un four à 800 °C. Cette technique s’utilise surtout pour les sables qui contiennent des résines et qui ne peuvent pas être traités efficacement par voie sèche.
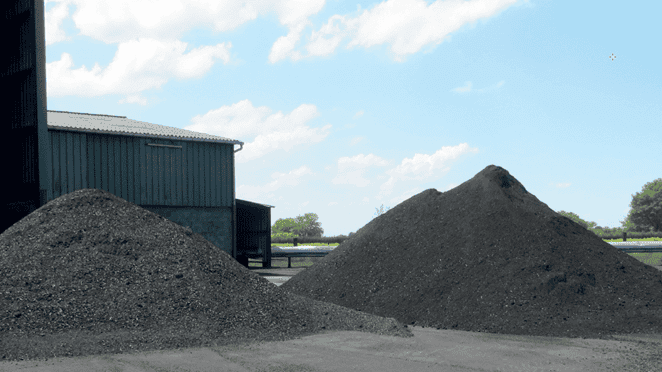
Étapes de recyclage de l’acier
Le recyclage de l’acier répond à une procédure bien précise. En effet, celui-ci est d’abord collecté et transporté vers un centre de tri, puis trié, traité et mis en paquets pour être redirigé vers une usine sidérurgique.
La collecte de l’acier
L’acier est récupéré depuis les différents sites industriels, déchetteries et centres de déconstruction et de démolition. Parfois, il subit un pré-tri sommaire avec l’aide de séparateurs magnétiques (grues à aimant). Il peut également être compacté ou découpé pour simplifier son transport en camion-benne. L’ensemble des aciers est alors transporté vers les centres de tri spécialisés en métaux et ferrailles.
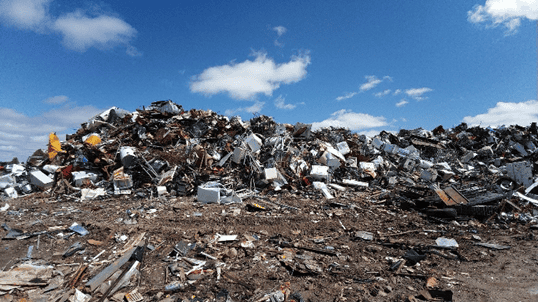
L’acier, selon sa nature, peut être collecté dans des lieux très différents :
- Dans des centres de déconstruction ou de démolition d’ouvrage. Les ferrailles de démolitions et les métaux sont ainsi prélevés grâce à des séparateurs magnétiques (grues avec aimant) ;
- Depuis des sites industriels, avec la récupération des rebuts de produits industriels, des chutes de découpes et de transformation, etc. ;
- A l’intérieur des casses automobiles, marines ou encore depuis des sites spécialisés dans la dépollution et la déconstruction d’avions, etc. ;
- Dans des déchetteries, comportant tous les emballages métalliques, les objets ménagers, etc.
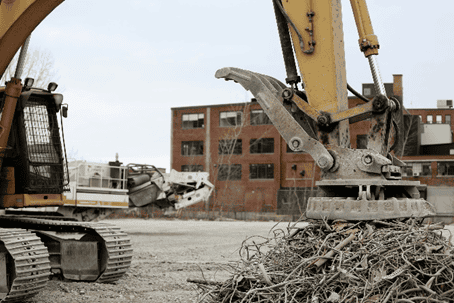
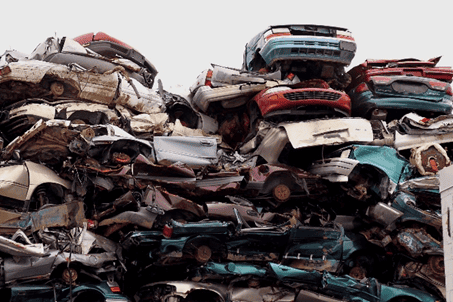
Le tri de l’acier et la séparation des métaux
À ce stade, l’acier se mélange avec des éléments de tous types et de toutes tailles. Il va donc falloir séparer l’acier ferreux (fonte ou acier) de l’acier non ferreux (cuivre, aluminium, etc.), mais également supprimer les autres déchets non métalliques. C’est le rôle du centre de tri. Comme l’acier est magnétique, il est facile de le séparer des autres déchets.
Plusieurs méthodes s’utilisent pour séparer et trier les métaux :
Les séparateurs à aimant permanent de type « Overband ».
Cette technique est simple mais efficace ! Un aimant suspendu au-dessus d’un convoyeur (tapis roulant) génère un puissant champ magnétique, séparant ainsi toutes les pièces métalliques du reste pour les rediriger vers un autre stockage.
Le triage par électroaimant.
Le principe de fonctionnement est similaire à celui de l’aimant « Overband », mais ici, le champ magnétique se créer par un courant électrique qui parcourt une bobine de fil de fer. Cependant, l’inconvénient de ce système est que l’électroaimant a tendance à s’échauffer, ce qui réduit légèrement son efficacité.
Le tri par poulie magnétique.
Dans ce système, un aimant permanent se positionne au centre du convoyeur. Cela permet aux pièces en métal de rester aimantées et de se déposer dans des bacs de tris situés sous le tapis du convoyeur. Les autres déchets non magnétiques tombent vers l’avant dans un autre bac de tri.
Le triage par tambour ou rouleau magnétique.
Les déchets sont dirigés soit par un convoyeur, soit par une trémie vibrante inclinée vers un tambour cylindrique en rotation qui comporte un aimant ou un électroaimant. Le tambour aimante le métal et le redirige par effet de rotation vers un compartiment spécifique.
Le tri par Machine à Courants de Foucault (MCF).
Les déchets circulent sur un convoyeur qui intègre un rotor magnétique. À l’intérieur de ce tube sont placés des aimants qui sont mis en rotation à grande vitesse. Ce mouvement des aimants crée un champ magnétique à variation rapide, appelé courants de Foucault. Ainsi, les métaux non ferreux (aluminium, cuivre, etc.) subissent un champ magnétique opposé qui les éjecte de l’autre côté du séparateur. Les déchets ordinaires (non magnétique) tombent par simple gravité dans un autre compartiment.
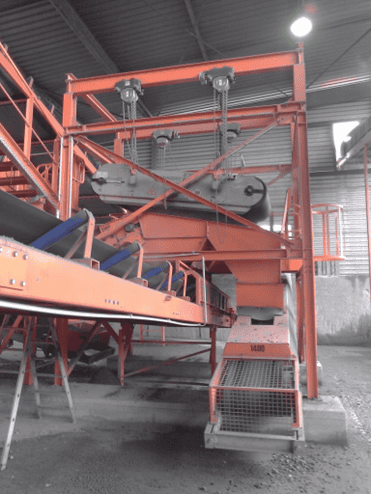
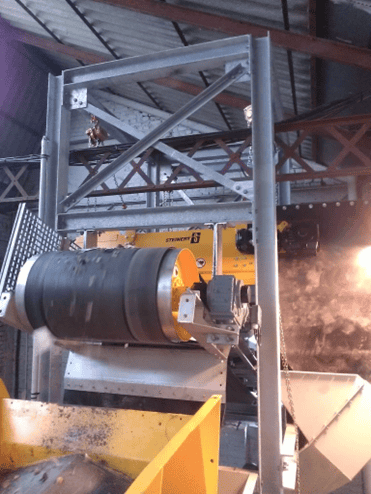
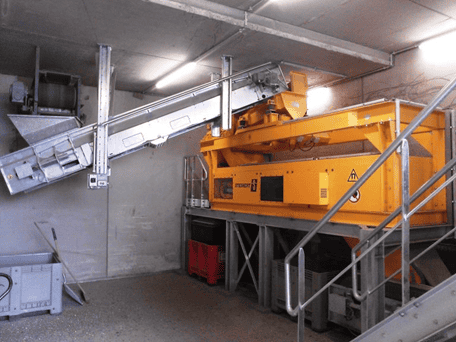
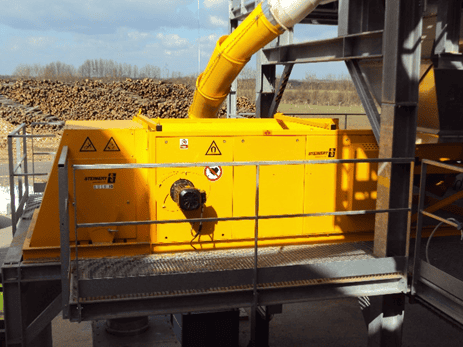
Les étapes de la valorisation de l’acier dans son cycle de recyclage
L’acier est désormais trié. Toutefois, pour pouvoir se recycler efficacement en usine sidérurgique, l’acier devra subir des transformations visant à le rendre plus compact et plus facilement transportable.
La réduction du volume
Plusieurs techniques s’utilise couramment pour réduire la taille de l’acier, selon son type :
- Le broyage. On envoie l’acier dans un broyeur, où deux axes rotatifs munis de marteaux le broient en sens inverse. L’acier en ressort sous forme de copeaux.
- Le compactage. On comprime les ferrailles et les emballages métalliques à l’aide d’un compacteur (presse), leur donnant ainsi une forme cubique, dite « balle ».
- Le ciselage. On cise les ferrailles lourdes, comme les rails de chemin de fer et les appareils électroménagers, à l’aide de cisailles hydrauliques qui découpent le métal en petits morceaux.
Etape de recyclage : La décontamination de l’acier
Certains aciers triés peuvent contenir des éléments indésirables, voire nocifs ou dangereux. Avant d’être réutilisés, ces derniers doivent être décontaminés dans des centres spécialisés. La décontamination s’obtient en pratiquant plusieurs opérations de fusion de l’acier en le chauffant à très haute température dans un four à arc électrique. Parfois, des produits de dilution sont rajoutés pour faciliter la purification de l’acier.
Le réemploi de l’acier recyclé : l’étape ultime
L’acier trié, compacté et nettoyé est désormais prêt à connaître une nouvelle vie. On le transporte alors vers une usine sidérurgique, où on le mélange avec de la fonte en fusion dans un convertisseur à oxygène. L’acier recyclé se réintroduit dans le cycle de fabrication de l’acier primaire. Redevenu liquide, il rejoint les ateliers d’affinage pour être laminé et transformé en nouveaux produits, tels que des bobines, des barres ou des fils. Ainsi, de la production au réemploi, la boucle est bouclée !